After gluing in the neck, we can finish off shaping the neck, heel and button. We then do the set-up, which involves making and installing the saddle, reaming the holes for the pegs and the button, cutting a sound post and bridge and finally stringing it up.
I never ceased to be amazed at how the tone of a new violin changes over the first few days as the stresses relieve and the instrument “gets used” to being a violin. When I first play it, it never sounds very good. You can tell whether it is going to be good or not but it is very hard to resist fooling around with the set-up to see if you can make it better. After 45 minutes, the tone improves 100%. Everything starts opening up a little bit. After several hours it is like a different instrument. This goes on for several days until the tone finally starts to stabilize.
It has been about a week now and I have to say “The Edward” is amazing! Maybe the best ever. The tone is full and powerful and very even across all of the strings. I can’t stop playing it. I’ll leave it in-the-white for a couple more weeks while I work on a bow commission but then I will take it down and varnish it. Below are some pictures of the completed instrument.
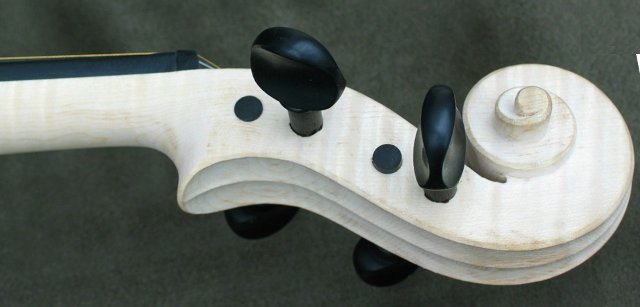
I am very pleased and I’m sure Ed will be as well.